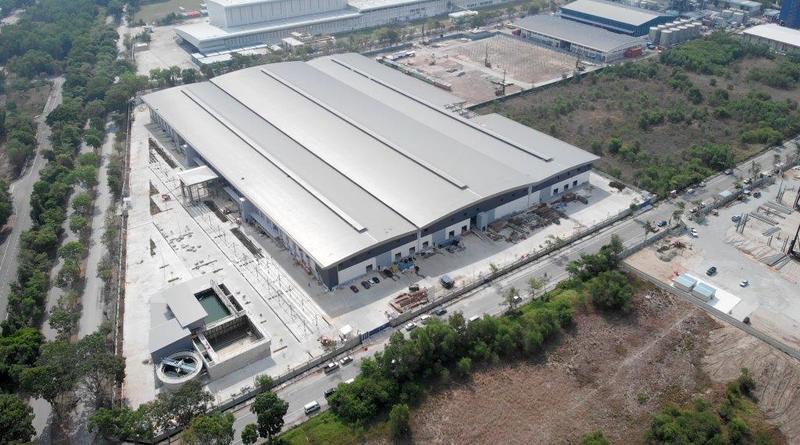
Ramly Food Industries’ new plant at Pulau Indah
Before Ramly Food Processing Sdn Bhd (Ramly) became the behemoth it is known today, it was but a small family business helmed by a husband-wife duo – Dato’ Dr Haji Ramly Mokni and Datin Hajjah Shala Siah Abdul Manap. The company, once known as Perusahaan Burger Ramly Mokni Sdn Bhd, aims to produce Halal, hygienic and quality products, including frankfurter, nuggets, meatballs, burger patties and even sauces such as chilli and mayonnaise as well as supplying to burger stalls nationwide.
Stroll along suburban streets in Malaysia and you will likely come across the Ramly brand, selling hot, juicy burgers that can even rival well-known fast-food restaurants. Believe it or not, Ramly started out by selling burgers in the very same food stalls before expanding in 1984. The company now encompasses various processing plants, and 10 subsidiaries, becoming a billion-dollar business and pride of the nation.
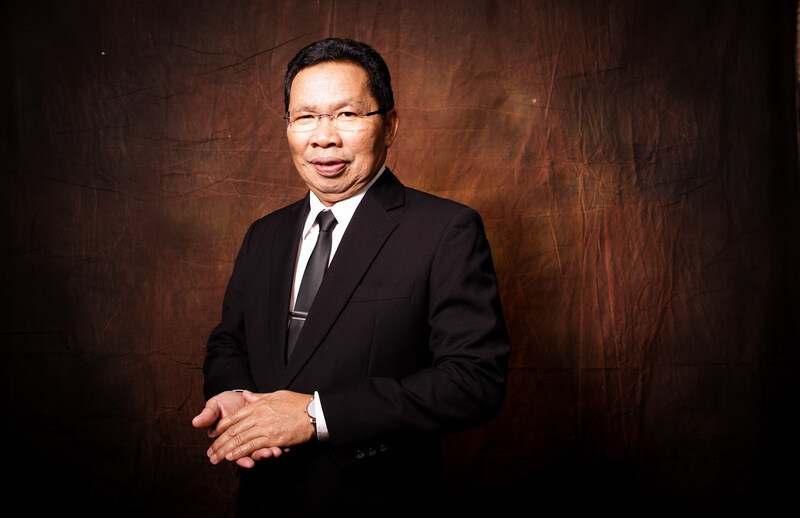
Dato’ Dr Haji Ramly Mokni, Founder and Managing Director of Ramly Group.
Path to Digitalisation
Dato’ Ramly realised the need to be flexible, fast, accurate and proactive as conventional industrialisation will not pave the way for the future. As demand for Ramly’s products began to surge, the decision to digitalise processes became more relevant than ever. Furthermore, machine manufacturers in Europe at that time heralded the arrival of Industry 4.0 (I4.0) as the next wave in the industrial sector.
Most of the industrial processes were done manually at the beginning, such as taking inventory of finished goods. This left a wide margin for human error such as missing products and expirations. The introduction of goods inventory system was meant to address this issue; however, staff training posed its own challenges as the sophisticated system was met with resistance.
A workaround was to hire a new team that was not already bogged by the inertia of familiarity. The team was screened to ensure that awareness and passion for I4.0 were already present. This was the impetus that propelled further adoption of smart technologies that would eventually improve flexibility, speed, productivity and quality.
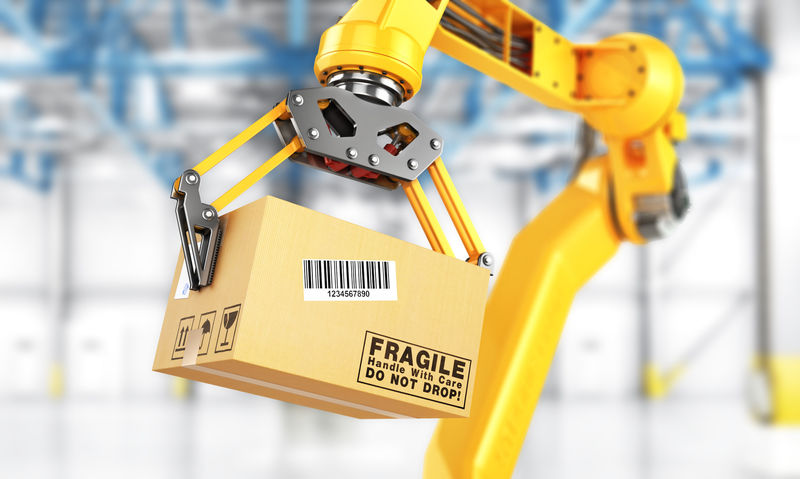
Endline packaging is done efficiently with minimal errors, thanks to robotic arms.
Utilising Smart Technology
In a high-octane production plant, the application of autonomous robots has observed a reduction in non-skilled human capital by 90%. Ramly’s mundane activities were undertaken by robotic arms, specifically in the end-line packaging, and sausage loading and unloading processes.
This frees up at least 100 workers in the packaging line and 20 workers in the loading and unloading bay to be assigned to high-value tasks. With autonomous robots, the company only require eight skilled workers to supervise the production line. Additionally, the installation of autonomous robots also decreased human error and improved customer satisfaction towards Ramly’s products.
The company’s production line also benefits from the Internet of Things (IoT) and reduced maintenance cost as well as machine downtime. The system works to alert the maintenance department of any errors and its precise location or scheduled routine maintenance. These translate to heightened productivity, efficiency and profitability for the company.
When it comes to maintenance, Augmented Reality (AR) acts as the key enabler for remote troubleshooting. AR overlays information and digital content in real-time on the physical world, all visible through an eyepiece. Through this technology, even engineers in their principal production plant are able to offer assistance and streamline corrective procedures.
The company adopts all these technologies to reach and maintain a maximum capacity of production, by maintaining uptime of machinery. The usage of predictive maintenance capacity to evaluate machine performance in real-time is crucial to keep up with rising demands.
Lending a Hand
The path to digitalisation and adoption of 4IR technologies is not a lonesome journey and the Malaysian authorities have been mandated to assist through various avenues.
Malaysian Development Bank, also known as the Bank Pembangunan Malaysia Berhad (BPMP), through the Ministry of Finance offers assistance via the Industry Digitalisation Transformation Fund (IDTF). The fund – an allocation of RM3.0 billion – is intended to accelerate the adoption of I4.0 related technologies in the manufacturing sector to benefit the national economy. Ramly is a recipient of the loan and it has bolstered the development of its new production plant in Pulau Indah.
IDTF offers Capital and Operational Expenditure for up to 15 years and 5 years respectively to companies that are registered and incorporated in Malaysia. Additionally, recipients of the loan will benefit from an interest subsidy of two per cent per annum, provided by the government. Any firms that offer technologies, looking to adopt technologies as part of their operations or construct infrastructure related to technology are eligible to apply.
Ramly thanks the Malaysian Digital Economy Corporation (MDEC) for their initiatives to help organisations attain their 4IR goals. Through close collaboration with MDEC, Ramly aims to realise the full potential of autonomous machinery in their Pulau Indah plant. The use of real-time custom reports and dashboards will enable the paperless collection of production data as well as allow for immediate response to performance issues.
In the Pipeline
In the era of digital marketing and burgeoning eCommerce platforms, Ramly’s momentum leaves them in a favourable position. The company looks to penetrate the market by launching its very own eCommerce platform to boost online sales. It looks to partner with existing online grocery platforms and sells products directly from local vendors to consumers, without the need for a middleman. It does not just stop there – the company further improves on its website functionality and user interface as it realises the importance of front-end customer engagement.
Through implementations of cyber-physical systems to monitor physical processes, leverage on data and automation, Ramly is positioned to develop a modular structure throughout its smart factories and make decentralised decisions to address issues and execute solutions without impediment.